Published date:
Heating long, heavy oil pipelines
As an alternative solution to the skin effect system, Heat Trace Limited proposed that a series resistance LONGLINE heat trace cable would provide a less expensive system – both in the purchase of materials and components and, more importantly, significantly reducing the installation costs.
Instead of welding carbon steel tubes to the pipe, a number of rectangular steel box sections would be strapped (not welded) over the anti-corrosion coated pipe during fabrication at the factory. Following this, a polyurethane foam thermal insulation and final outer cladding would be added.
When the fully assembled pipe stalks arrived at site, they were welded together as normal and the anticorrosion coating repaired as necessary. No further
welding operations were required.
A total of nine rectangular box sections were used on the flow pipeline for this project, to accommodate 3 × 3 phase heating circuits. The box sections do not act as part of the actual heating system and are simply used as a method to get the series resistance heating cables onto the pipe, beneath the thermal insulation layer.
The methods for pulling, or pushing, the cables through the box section can vary from project to project. This can be undertaken either by feeding pulling ropes
inside of the box section and pulling the cable through, or by pushing the cable through. This project allowed an installation rate of 20 m/min. of cable to push
the cable through the box section by hand, with 400 m lengths being successfully installed in a single operation.
On other projects, a capstan winch and pulling ropes have been utilised. This increases the installation rate to over 40 m/min. of cable.
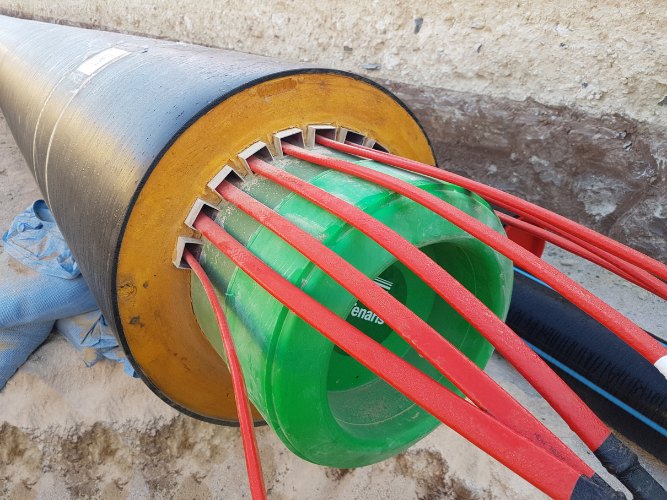
Socotherm S.p.a. requested many physical tests and computational FEA studies to prove that the technology would provide the required solution of heating the
HFO pipelines up to the required temperature over a 48 hr period. After successfully completing a number of different tests, Socotherm S.p.a. concluded that the series LONGLINE solution being proposed had many commercial, technical and installation benefits and advantages over a skin trace system.
For this particular project, due to the tourist season, the installation team were limited to only installing approximately 400 m of pipe at a time. However, the cables were easily installed within half a day.
Once all the the LONGLINE cables had been installed into their respective box sections, tests were undertaken on each cable section before splicing to the next cable This was followed by further electrical insulation resistance tests.
Once all of the tests had proved positive, the heating cable field joints, together with the sections where the cable transited the pipe joint were covered over with thermal insulation, then cladding was applied and the pipe trench backfilled.
In a similar fashion, the cables on the subsea section of pre-insulated pipeline were installed through the box sections and water-stops. Once completed, the 600 m subsea section of pipeline was towed out to sea and lowered into position. The pipeline was then further protected with a concrete cover to protect and secure it in place on the seabed.
The completed fuel oil tanker offloading system was commissioned in April 2018 and successfully received the first oil deliveries to the site in May 2018
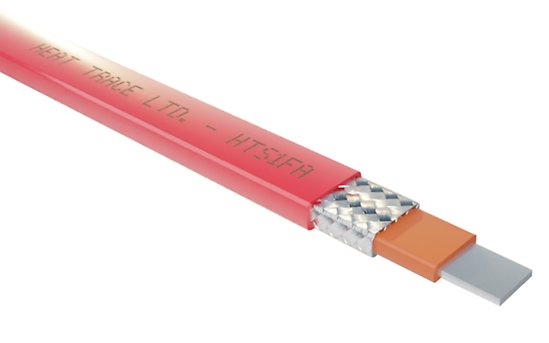
The LONGLINE system can be used in many applications, where elevated temperatures are required in order to mitigate flow assurance problems in multi-kilometre pipelines. A similar system was used on the world’s first electrically trace heated, reeled pipe-in-pipe system (ETHPIP) for a 6.5 km heated subsea gas condensate tieback, from the Islay wellhead to the Forvie manifold in the North Sea, at a depth of approximately 120 m.
One of the earliest LONGLINE heating systems used with pre-insulated pipe sections was installed in the 1980s in New Zealand. This was for approximately 30 km of buried, pre-insulated crude oil pipelines from onshore wellheads to a central gathering station.
With the savings that are achievable with the LONGLINE system, when compared with a skin effect heating system, many pipeline heating applications exist in upstream, midstream and downstream areas.
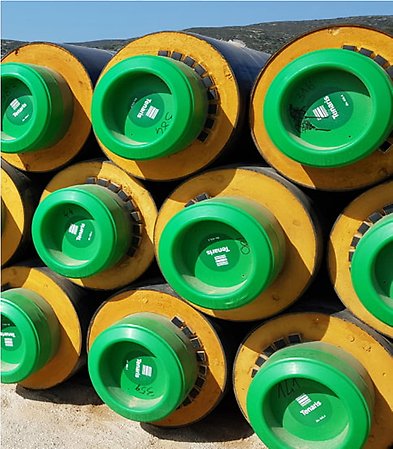
The capability of LONGLINE heaters changed when, to meet the demands of long pipeline operators, the trace heating world’s first continuous metal extrusion facility was designed and built. This unique facility can produce virtually endless lengths of low resistance profile conductors, as well as continuous metallic over-jackets.
It is now possible to produce heating circuits much longer than existing systems, at significantly lower costs.
The metallic over-jacket results in a heating cable with massively increased mechanical strength when compared
with the relatively low strength of alternative systems. This enables the LONGLINE cables to be pulled greater
distances without damage, thus minimising the number of field cable joints. Now, a single electrical power supply
point may feed LONGLINE circuits of approximately 50 km, such that power supply point intervals of 100 km are possible for centre-fed heating circuits. To achieve these longer circuit lengths, supply voltage capabilities now extend up to 6.6 kV. Investment has also continued in conductor jointing techniques, recognising that joints are the potentially vulnerable point of any heating installation.
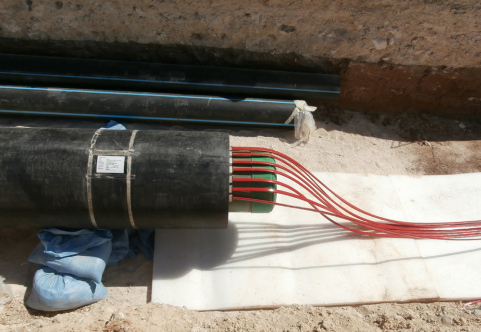
The capability now exists for insulated and heated
pipelines for both onshore and offshore pipelines that
transport hydrocarbon products over multi-kilometre
distances. Also, long heating circuits ensure a minimum
number of power supply points, resulting in significant
CAPEX savings. Additionally, the LONGLINE heating system is easy to install without damaging or affecting the corrosion resistant pipe coating.
The original LONGLINE heating system, launched by Heat Trace Limited more than 30 years ago, has been refined, improved and upgraded into a variety of heating cables, from which the most appropriate type may be selected to suit any particular application.
Other applications
Applications may include, but are not limited to:
- Subsea tiebacks.
- Offshore/onshore tanker offloading pipelines.
- Oil storage and distribution facilities.
- Multi-kilometre cross-country pipelines.
- Offshore crude oil export terminals.