Long Buried Pipelines (up to 50km)
The Problem
The heat tracing of long buried pipelines is an application in which Heat Trace Limited have unique experience. We have developed a system which satisfies all operational, installation and system life requirements and which is now proven under operating conditions over many years.
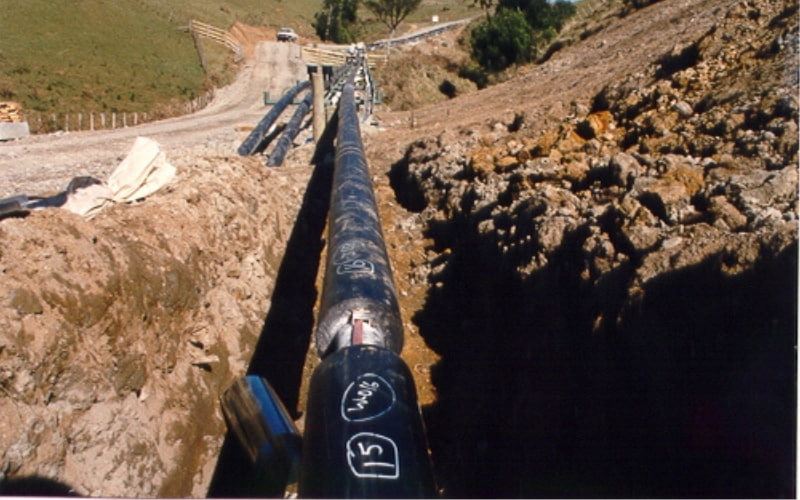
Installed Electrical Loads
Heat losses from a buried pipe remain substantially constant. A designer will propose an installed load having excess heat capacity as he must anticipate worst ground conditions which may never actually prevail.
Unless controlled, this excess heat could result in system failure or reliabilty problems.
Electrical Supplies
Often the most important consideration when heating long pipelines is the number and location of electrical supplies. They are normally available at the pipe ends. The cost of providing intermediate supplies is prohibitive, so heating circuits must be designed for long routes lengths.
The Need for Power & Energy Management
Long pipelines typically require hundreds of kilowatts to maintain pumpable temperatures. Power/Energy management minimises operating costs and maximum demand, and eliminates expansion/contraction which could result in failure of the thermal insulation or heater.
Reliability
Failure of a multi-kilometer heating circuit renders the complete pipeline useless. Thus, system reliability and life is much more important than for in-plant heat tracing.
The Solution
Low resistance conductors, 3 phase star connected produce long circuits. Conductor sizes and applied voltage are adjusted to provide the required length and output. Compared with round conductors, flat foils are outstandingly thermally efficient due to their large surface area and they are much more flexible.
A single Longline HTS3F tracer having 3 conductors is suitable for shorter circuits (up to 1km).
Multiple large single conductor Longline HTS1F tracer cater for longer circuits (up to 5km).
View the Heat Trace Cable Range Max Exposure Temperature & Output Capability Graph:
Conventional Control
Long heated pipelines are usually controlled by a line thermostat operating a large contactor having a limited life - a 20 minute ON/OFF switching cycle may result in contact failure in less than two years.
To extend contact life, the thermostat switch differential is often widened to reduce the switching frequency. This produces poor efficiency under no flow conditions. When the product flows, energy wastage is 100% because the controller switch off temperature is never reached and so the load remains permanently energised.
ON/OFF thermal cycling of the piping and its system eventually results in, at best, damages to the thermal insulation system and possible system failure.
For a high integrity long pipeline installation, it is recommended to use PLC or other electronic control which utilises PID control.